Rubber keypads are widely used in the "push-button" facilities found throughout in our daily life, such as personal computer keyboards, calculators, remote controllers, cellular phone/mobile phones, multi- functional telephones, multi-functional CB radios, car-stereos, cameras and answering machines.
|
Materials The hardness of silicone rubber can be graded between 30 to 70 shore A. Suggested hardness for silicone rubber keypads is 40 to 60 shore A depending on customers’ requirements for actuation force, tactile response and life. Higher hardness rubber keypads offer higher actuation force and snap ratio but shorter life. Lower hardness rubber keypads have lower actuation force and snap ratio but longer life. Silicone rubber is available in flame classifications of UL94HB and UL94V0, and the flame classification of most silicone rubber used for keypads is UL94HB. |
Contact Resistance Silicone rubber keypads can be co-molded with carbon impregnated silicone pills (carbon pills), gold plated pills and metal pills according to customers’ requirements. Due to the low cost of production and acceptable resistance (less than 100 ohms), most rubber keypads are co-molded with carbon pills. |
Rubber Color The nature color of raw silicone rubber material is translucent white. Raw materials are blended with silicone based color pigments to obtain the color needed by the customer, and it can even be blended with phosphorescent materials to glow in dark. |
|

|
|
|
Force Range(gm) |
Stroke Range(m/m) |
Cycle Lifex10(Times) |
Typical Uses |
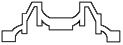
|
40~130 |
0.6~2.5 |
3000~20000
long-life |
Presonal Computer,
Main frame Computer |
Figure A |
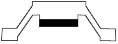
|
50~350 |
0.5~3.0 |
500~2000 |
Telephone,Remote
Controller,Caculator,TV game.........etc |
Figure B |
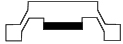
|
30~250 |
0.7~1.5 |
500~2000 |
Telephone,Remote
Controller,TV game,
Caculator Translator
Machine...etc... |
Figure C |
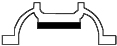
|
30~180 |
0.5~3.0 |
1000~3600 |
Remote Controller,
Toys office Machine,
Measurement
Instrument |
Figure D |
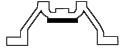
|
30~180 |
1.5~4.0 |
5000~10000
long-life |
Com puter
Type writer....etc |
Figure E |
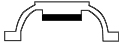
|
30~200 |
1.0~2.5 |
2000~20000
long-life |
Telephone,typewriter
Test Instrument
Com puter....etc... |
Figure F |
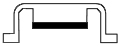
|
20~250 |
0.2~1.0 |
500~10000 |
Remote Controller,
Calculator, typewriter
Com puter....etc... |
Figure G |
|
|
Actuation Force / Travel The force / travel diagram is the definition of characteristic feel for depressing the keypad button. |
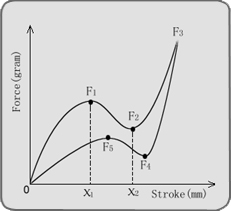
|
|
F1:PEAK FORCE
F2:CONTACT FORCE
F3: UNLITIMED
F4: RETURN FORCE
F5: MAX. RETURN FORCE |
X1:PEAK STROKE
X2: CONTACT STROKE |
0-F1-F2-F3:PRESS CURVE
0-F3-F4-F5: ELASTIC CURVE |
|
A complete examples of actuation force specification is as follows : |
|
Actuation(F1):
Travel:
Tactile feel:
Return force: |
150 35grams
1.0 0.1m/m
35-50%(snap ratio)
Minimun50 grams |
Note:For reference only |
2. KEYPAD DESIGN QUIDE

INDEXES |
VALUE |
Contact resistance: |
200 ohm maximum with 150 grams typical |
Life: |

|
Contact bounce: |
10 Msec.maximum |
Insulation resistance: |
100 Mohm at 250v DC |
Maximum contact rating: |
24v DC 100mA |
Dielectric strength: |
15 kv/mm |
Operation temperature: |
-40 ~150 |
Storage temperature: |
-50 ~175 |
Travel: |
0.8mm ~1.2mm typical |
Material hardness: |
50 5 shore A typical |

 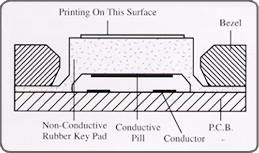

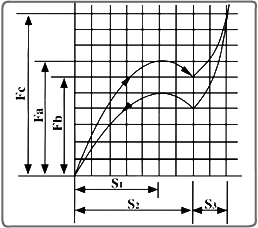
Fa:Actuation Force |
|
S1:Actuacing distance |
Fb:Tactile feedback |
|
S2:Travel distance |
Fc:Overall travel force |
|
S3:Overall travel distance |

Standard Size: round shape, 1.50, 2.00, 2.50,to 8.00mm.
Thickness: 0.60mm±0.10mm.
Special shape or size is available with an extra tooling charge.

PARAMETER |
CONDUCTOR |
INSULATOR |
Specific gravity(25 ): |
1.16 - 1.20 |
1.09 - 1.18 |
Material hardness (shore A) |
60 - 70 5 |
30 - 80 5 |
Tensile strength  |
60 |
75 |
Elongation at break: |
265% |
300% |
Tear strength  |
9 |
15 |

Under 30 mm |
+/- 0.1mm |
30 - 50 mm |
+/- 0.2mm |
50 - 100 mm |
+/- 0.3mm |
100 - 150 mm |
+/- 0.4mm |
150 - 200 mm |
+/- 0.5mm |
Over 200 mm |
+/- 0.8mm |

Optimum actuation force: 80g to 150g
Optimum stroke (travel distance): 0.80mm to 1.50mm

1. Stroke 0.80mm
2. Add stabilizing posts on the key's bottom side
3. Short length actuating membrane
4. 40°angle for actuating membrane
5. Tactile ratio is 30% of total travel range
3. SILKSCREEN PRINTING AND COATING
Silk-screen Printing Printing colors can be multiple by using multiple printing process. Each color requires one printing process. The optimum keytop that required for printing has to be flat keytops. However, some curvature keytops can also be printed.
Spray Printing with Back-lighted Legends After molding translucent material for silicone rubber keypads, the material is spray painted with black and white ink on the front side. A laser is used to cut out or chemically etch legends on keytops to form a back lighted legend effect with a Fiber Optic or EL lamp under the keypad.
PU Coating Silicone rubber keypads can also be spray coated with PU resin to provide absolute life time abrasion resistance and oil resistance satisfaction. This important technique has already been successful developed.
Hard Coating A screen-printing or spray-painting process is used to coat an additional protective clear silicone ink on the color screened keytops. This increases the abrasion life of the screened color ink.
Epoxy Coating Silicone rubber keypads can be coated with a layer of epoxy resin to form a hard (or medium hard) top and feeling like plastic appearance, and provides screen text protection.
4. PRODUCTS APPLICATION DIAGRAM
FIELDS OF INDUSTIES |
APPLICATIONS |
Household Electric Appliances |
Rubber-made parts around high-voltage |
Circuit in color TV sets |
Anode caps |
Defrosters in refrigerators |
Hot air brushes |
Steam irons parts |
Front door gaskets and turn belts of microwave ovens |
Packing of steam kettle valve, steam pipe, rice cooker, electric pot, pressure kettle. |
|
|
Electric Wires |
Lead wires for motors and electric appliances |
Heater wires in refrigerators |
Ignition wires |
Insulated cables for atomic power plant |
|
|
Business Machines |
Rubber contacts in pocket electronic |
Calculators and keyboards |
Emi gaskets |
Rubber rollers in ppc copying machines |
Platen rollers in telecopier machines |
Platen rollers in printers |
Facsimile rollers |
|
|
Hobby Goods |
Goggles, snorkels |
Mouthpieces, goggle bands |
|
|
Medical |
Rubber stoppers in medical instruments |
Rubber parts attached to spectacles |
|
|
Cosmetics |
Spongy puff in medical instruments |
Rubber brush attached to hair-curlers |
|
|
LIMs (Liquid type silicone injection molding) |
O-rings, diaphragm, |
Capping, connector packing |
Rubber rollers |
5. PRODUCTION PROCESS AND QUALITY CONTROL
At SICON, our staff and management team share the same company goals and work well together on achieving those goalds. Because of their cooperation and focus on achieving quality and efficiency, SICON managed to implement ISO9002 requiements in only 140 days while most other manufacturing firms took over 6 months.
However, we do not consider the ISO9002 certification and indicator showing that we have done enough to achieve quality. We consider endless pursuit for progress is only way we can remain competitive and provide high quality products to our customers.
Implementing and maintaining quality control in our production process is SICON's first priority. Our staff closely follows company policy and procedures throughout the production process such as usage of quality raw materials, accuracy of the molding, precision of the silkscreen printing, and details of the final inspection.
By using in-house automated machinery with 100% in-process-inspection and the latest silkscreen techniques, we have obtained a high yield rate and efficiency to provide our customers competitive prices and desired quantity. That is why we have attracted large stable customers who demand quality and capacity for high volume orders at competitive prices.
Products show
|